Seyedmorteza Khatibmasjedi has a conflicted relationship with concrete.
"I was always thinking concrete is the best material in the world," says the University of Miami civil engineering Ph.D student. (He goes by Morteza Khatib.) "All those skyscrapers, all those high bridges -- all of them are made out of concrete."
"We make a kind of soupy material," Khatib says. "After 10 hours... it can hold two cars."
But, he says, "I was working on concrete without paying attention to the environmental impacts."
Concrete's strength and versatility make it a highly desirable building material. Khatib says there's roughly enough manufactured each year for every single person on the planet to get a three-foot-tall cube and still have about a billion cubes left over. Industry analysts routinely describe it as the second- most widely used material in the world, ranking only behind water.
And water is part of concrete's problem.
"It has to be basically the water that people can drink," Khatib says, adding that based on a 2004 Columbia University study, concrete production uses 180 billion gallons of freshwater per year. He says that water could be going to people who are suffering from water shortages.
The problems with conventional concrete
The ingredient list for concrete is short: sand, water, cement and coarse aggregate (which is basically rock). Builders like the simplicity of these materials, but collecting and preparing them for concrete can do serious environmental damage.
Superheating limestone to make cement burns fossil fuels and can release pollutants into the air, (although UCLA researchers have figured out a way to make cement production carbon-neutral).
Mining rivers for sand can interfere with freshwater supplies and damage fragile ecosystems.
And then there’s the massive amount of freshwater required for the concrete mixture.
Many concrete structures are constructed around steel rebar, and salt in the concrete could cause the steel to corrode. So the water used in conventional concrete has to be fresh, says Steve Nolan, a structures and designs engineer for the Florida Department of Transportation. He compares rebar corrosion to the rusting that occurs if you leave a paperclip in saltwater.
“What happens to the steel when it corrodes is it expands. Then as it expands, it puts force on the surrounding concrete, tends to crack the concrete,” Nolan says. “That just allows more saltwater to come in and you get this domino effect of accelerated deterioration.”
That’s why builders haven’t historically been able to use seawater when they make concrete. They can’t use recycled concrete because it could be contaminated by seawater or — in some parts of the country — the salt that’s put on roads. And they have to wash sand with freshwater before they can mix it in.
Khatib says each ton of concrete uses 18 gallons of freshwater to make. Columbia University researchers report the concrete industry makes more than 10 billion tons of concrete per year.
So each year, the world uses more than 180 billion gallons of freshwater — enough to fill more than 272,000 Olympic-sized swimming pools — to make concrete. That doesn’t include the freshwater used to wash the sand.
"The problem is that lab durability and lab aging is not the same as real aging" - Francisco De Caso
Simultaneously, 783 million people worldwide lack access to clean drinking water, according to the United Nations.
“There is enough water available to meet the world’s growing needs, but not without dramatically changing the way water is used, managed and shared,” staff from the World Water Assessment Programme wrote in a prologue to a 2015 UN report, “Water For A Sustainable World.” “This is where the bulk of the action is required in order to achieve a water-secure world.”
Introducing SEACON
To address concrete’s various sustainability issues, a team of researchers at the University of Miami has worked with industry partners elsewhere in the U.S. and in Italy to develop a new type of concrete made from recycled material and seawater. They’re calling it SEACON, as in “seawater concrete.”
Because of the corrosion issue, concrete made from recycled materials and seawater wouldn’t work with normal steel rebar. So the researchers are also testing a new kind of rebar, made primarily of glass fibers.
Khatib and Francisco De Caso, an associate UM scientist, show off their work in a structures and materials lab on the university’s Coral Gables campus. Hefting a piece of glass-based rebar in one hand and traditional steel rebar in the other, Khatib explains how glass rebar is lighter and stronger than steel rebar.
Because glass rebar is not susceptible to corrosion from salt, they say it shouldn’t have to be repaired or replaced as often as steel. They’re testing that in a room that’s kind of like a time machine: They put the glass rebar into saltwater-filled chambers or they freeze and thaw it every day for a year.
“One year in this room is equal to 50 years to 100 years outside,” Khatib says.
De Caso adds, "At different temperatures, you basically accelerate the aging of the materials. Otherwise we'd need to wait 100 years, and I don't think I'd be around for that."
So far, they say, the rebar’s holding up. But, De Caso adds, “The problem is that lab durability and lab aging is not the same as real aging.”
That's one reason SEACON’s project manager at UM, Dr. Antonio Nanni, reached out to Steve Nolan and the Florida Department of Transportation to use SEACON and glass rebar to build the new Halls River Bridge in Homosassa on Florida’s west coast.
It’s still kind of an experiment: Nolan says instead of using west coast saltwater for the concrete, builders are trucking in saltwater from Miami to make sure the amount of salt is consistent with what UM tested. FDOT isn’t using SEACON for the bridge deck, where the cars drive, because the department wanted more safety testing first. And the glass rebar costs more than steel to install -- by as much as 15 percent.
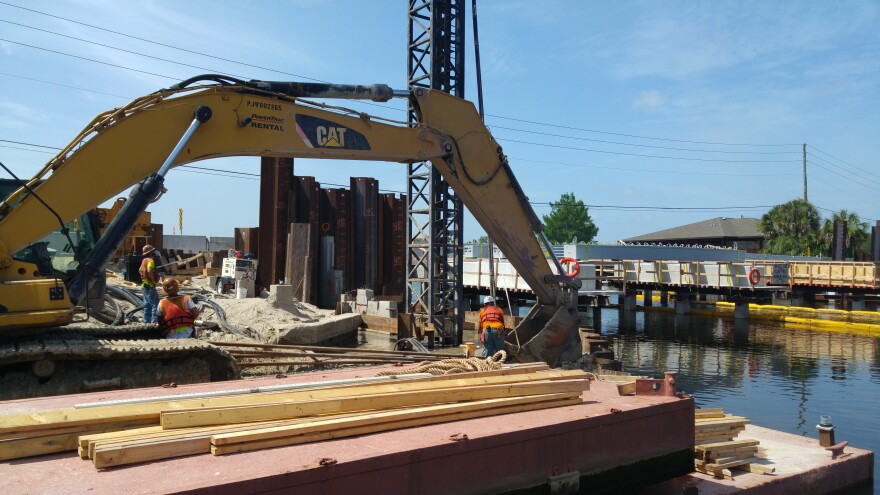
But, Nolan says, FDOT is willing to pay more up front if it means avoiding expensive restoration projects in 30 or 50 years. And he says he’s excited that concrete structures built with glass-based rebar might be more resilient to rising seas.
“If we can guarantee the longevity of the supporting structure, then over time, if there is a need to raise [supports], you can build on top of them with no concerns about degradation,” he says. “I think it’s a great solution for those coastal challenges.”
SEACON, on the other hand, may become a victim of its own success.
“SEACON is basically a surrogate for long-term durability testing. We get what are perceived as the ‘problematic components’ directly into the concrete,” Nolan explains. What SEACON has shown, he says, is that with the right rebar, it’s OK if there’s salt in concrete structures.
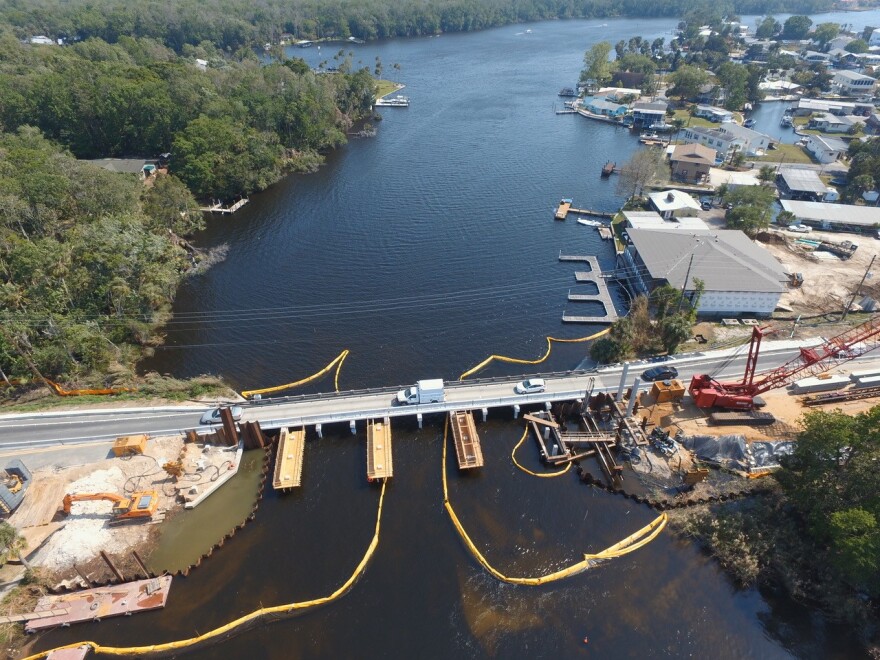
That means FDOT, regulatory agencies and builders can relax the standards for salt in concrete. So there’s no need to wash sand with freshwater or eschew recycled concrete — but there’s also no need to bring in seawater to use in the concrete mixture. (For non-coastal areas, Nolan points out, that doesn’t make financial sense anyway: It’s been costly and logistically challenging for FDOT to get saltwater from Miami to Homosassa, and that’s just from one side of Florida to the other.)
Nanni, the researcher who’s managing the project at UM, says that’s OK.
“More than seawater… we are advocating that the limitation on chloride in concrete is not necessarily a wise limitation. Provided that you don’t use steel reinforcement, that limitation is artificial. And there’s an extraordinary number of benefits that can be attained if we remove the chloride limits.”
He adds: “I think the writing is on the wall for many reasons.”
The Halls River Bridge in Homosassa is up for an international award at a composite materials exposition in Orlando in September. The bridge is expected to be completed in April.
A photo caption in this story has been corrected: The Fate Bridge at the University of Miami was built with glass-based rebar, but not concrete made with seawater. It uses conventional concrete.